Johannes Tiefenthaler: "We are hoping to shape the future of concrete and to make the material climate-neutral."
- Alumni Portraits
- Process Alumni
ETH alumnus Johannes Tiefenthaler has a Master's in Process Engineering. He is currently working on his PhD, yet in 2019 he found the time set up Neustark, a company which stores CO2 in concrete and aims to supply zero-carbon concrete. He talks to us about his career to date and how close he currently is to achieving his goal.
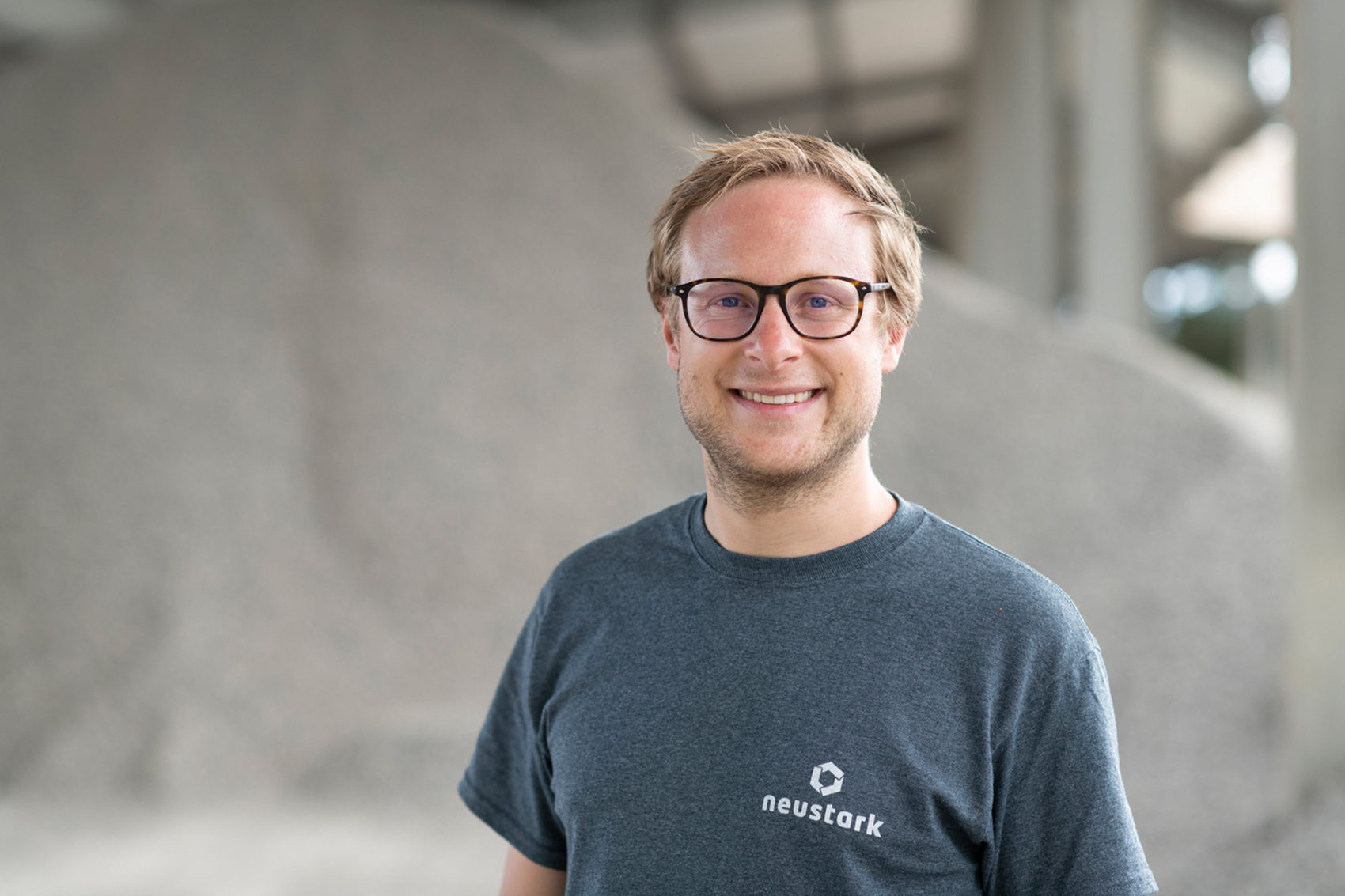
When you were a kid, what did you want to be?
I didn’t have a specific dream job. As a child, I was very curious and enjoyed spending a lot of time outdoors. I explored secret paths, gullies and watercourses near our home. It was always an adventure and I was the explorer.
You have a Bachelor’s in Mechanical Engineering and a Master’s in Process Engineering from ETH. Why did you choose to study at ETH?
I was good at subjects like mathematics and physics that require logical thought processes. But I didn't want to exclude the practical element. And environmental matters were important to me. Engineering was therefore the obvious solution. Zurich offered me both the opportunity to be close to nature with its mountains and lakes and a technical university. As a result, I applied to ETH Zurich and was accepted to study mechanical engineering and process engineering.
Over the course of my time at ETH, I became increasingly interested in energy because I associated it with climate protection. Given my interest, I then attended a lecture by Professor Mazzotti about technologies that can prevent the emission of greenhouse gases, which are also produced when using renewable energies. This is how I discovered the field of carbon capture and storage (CCS). I learnt that by using this technology we can turn back the "climate clock" through what are known as negative emissions. I was fascinated by the challenge of moving industry towards climate neutrality and thereby solving the climate problem.
Many climate-focused technologies suffer from the same thing: there is no market for them under the current financial conditions so they create limited added value and have no large-scale impact. If technologies aren't being used, there is no learning curve – and they don't get any cheaper.
In 2017, things came to a crux for CCS. Initial investment costs were high, emissions-trading systems didn't provide industry with financial incentives to act to reduce their emissions, the market was not proving willing to pay more for climate-friendly products and the infrastructure to do so didn’t exist in Europe. Even though the 2015 Paris climate agreement clearly spelt out that CCS is essential in meeting the climate targets it set out, the technology was a political hot potato.
Despite all this, I was convinced that we could solve this chicken and egg problem. The key was to demonstrate the first steps on a small scale. We needed to show that the technology was available to the market for less financial risk. If the market accepted the solution, we would have won.
You are currently working on your PhD at the Institute for Energy and Process Engineering. What are you researching now?
In my master’s dissertation, I researched CO2 mineralisation for the first time. For greenhouse gases not to harm the climate, we need to keep them out of the atmosphere. There are two ways of doing this on a meaningful scale: geological storage or mineralisation to form a carbonate rock. Mineralisation means converting CO2 with the aid of magnesium or calcium silicate, so-called precursors, into carbonate rock such as dolomite or limestone. Roughly 80 percent of the world’s carbon can be found in limestone and dolomite. In our laboratory, we mainly used magnesium silicates as the precursors for storing CO2.
Transforming CO2 into carbonate rock provides a permanent storage solution. If we are to use magnesium silicate as the precursor, we need to set up a brand new industry for this process. The material has to be mined, crushed, thermally activated and transported to the mineralisation plant. Finally, it enters the ultimate storage phase or is used in industry.
In 2017, Jura Materials approached Professor Mazzotti to find out whether concrete debris could be used to store CO2. Concrete debris and many other industrial mineral waste streams contain calcium in an oxide, hydroxide or silicate form, which is high reactive and bonds CO2 easily as limestone. In my master’s dissertation I developed my first process for storing CO2 in concrete debris. However, it was still a long way off suitability for use on an industrial scale. But at the time, that wasn't what I was focused on.
During this time, I came to realise that mineralising CO2 in concrete granulate was a process that could be used commercially under today’s conditions. In other words, it would create real added value.
I pitched the idea to Professor Mazzotti of continuing my work to develop a mineralisation technology as part of a PhD and then to commercialise the process using an ETH spin-off. He was happy to embark on this adventure provided that the technological development came up to the scientific standards of ETH Zurich.
At the same time, Valentin Gutknecht had had similar thoughts but he was concentrating on the question of a market. We met up and made a good team, bringing different content and personalities to the table. We were able to drive forward development of the mineralisation value creation chain and the market at the same time and aligned our work accordingly.
In 2019, you and Valentin Gutknecht founded Neustark. What does the company do and what motivates you?
The raw materials for concrete are easy to obtain and are relatively cheap. Concrete is also easily processed, has many different applications and produces incredible structural properties. A global industry encompassing a lot of knowledge has grown up around this product. Given the huge amount of concrete used in the construction industry, its production has a significant impact on global greenhouse gas emissions. The sector will have to address this problem over the next few years.
We are hoping to shape the future of concrete and to make the material climate-neutral. Our strategy is to find a solution which can be used right now. Our goal is net zero and any effective reduction is important. We therefore launched an initial technology, including its value creation chain. We are able to store 10 kilograms of CO2 per ton of concrete debris. All Swiss recycling companies working with concrete debris can use this technology. We’re still taking baby steps. Demand for this solution in Switzerland and its closest neighbours is huge. More and more building sites are explicitly requiring the concrete used to have as small a carbon footprint as possible. This is providing concrete factories with an incentive to supply concrete containing aggregate enriched with CO2.
What is the next step for Neustark? What are your plans for the future?
We are currently running a mobile facility to allow concrete factories to try out our technology and test the concrete on the market. Every week, this facility is able to enrich up to 1000 tons of concrete granulate with CO2 and it runs with the equipment already used by concrete factories. At the same time, we are developing stationary facilities to improve environmental performance and cost-effectiveness.
As part of a project funded by Innosuisse, we are working with ETH Zurich and Jura Materials to develop another technology, which aims to make carbon-free concrete possible. A pilot plant will be up and running this summer. For us, carbon-free concrete means that all the atmospheric emissions resulting from the production process are removed and stored in the concrete.
Once carbon-free concrete has established itself on the market, we will have sufficient confidence to invest in further decarbonisation steps. For the process to be viable in the long term, it is also important that all stakeholders in the value creation chain can benefit from added value.
What advice would you give anyone studying at ETH today?
You learn a lot of the basics at ETH Zurich. You also have the opportunity to specialise in individual topics. Most importantly, you learn how to quickly familiarise yourself with new topics. During my time at ETH, I wasn't aware of how specialised I was. Building the first facility at Neustark opened my eyes because as a process engineer I was more familiar with the chemical process and less so with how to construct a facility and select all the components. In this respect, I think it’s important to concentrate on your own strengths and make up for any gaps in your skills by collaborating with others. This is key to making rapid progress and is fun too.